![]()
Aside from the obvious cost avoidance we gain by leveraging the inventory functionality Labguru offers, the biggest ROI we’ve seen is in the ability to leverage the Form Element functionality within a protocol to track our processes.
Adarza BioSystems, Inc. is a biotechnology company pioneering a label-free platform technology that enables the simultaneous detection of hundreds of analytes in a single drop of fluid. Transformed by the company’s experienced leadership team spanning multiple industries, Adarza’s first-to-market products will include a fully automated bench-top instrument with extensive analytical power as well as a suite of protein array assays and custom assay services. Much like the first gene-chips that enabled multiplexed genomics analysis, Adarza’s multiplex protein array platform will fundamentally disrupt the field of proteomics research by providing an easy workflow solution, from assay to analysis, for the drug discovery and clinical research industries. The initial consumable offerings will span large proteomics screening to smaller, validated arrays as well as “made-to-order” custom arrays. Given the flexibility of the technology, detection of nucleic acids, as well as viruses, bacteria and allergens is also possible which will help Adarza expand into other industries and clinical diagnostics. Adarza’s end users span all their functional teams from administration to engineering.
Adarza Biosystems, Inc., located in Maryland Heights, Missouri, currently employs 35 people out of which 22 use Labguru.
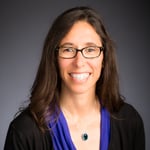
We interviewed Nanette Langevin, the Director of Quality Assurance and Control. Her job is to ensure Adarza develops and manufactures a product that allows their customers to deliver consistent, accurate results. Together with Anirudh Eswar, Quality Assurance, and Control Associate, their primary focus is to build a quality management system that enables them to standardize Adarza’s processes and track and measure their products so that they meet their quality deliverables. This system allows them to quickly detect when defects occur, allowing them to discover opportunities to continually improve internal processes.
Tell us what your lab does. What kind of techniques do you use in your kind of research?
Nanette: Our laboratory can be divided into two parts. The Manufacturing team produces the consumables for our product while our Research and Development team optimizes the chemistry for the consumables.
The manufacturing team uses automation to produce a highly uniform substrate for our proteins to bind. We use several kinds of highly technical measurement systems to ensure our product meets stringent specifications. Our Engineering team partners with the Manufacturing team to provide us with engineering solutions as well as regular preventative maintenance. The Manufacturing team’s product, custom consumables, are produced in a high-throughput fashion requiring us to capture large amounts of data accurately and depend on well-maintained equipment.
The second part of our lab is comprised of the Research and Development team. This group is composed of scientists ensuring our assays meet industry standards. They screen several targets and optimize conditions to contribute to our final product. This team also uses automation, specialized instrumentation, and custom software to perform their work.
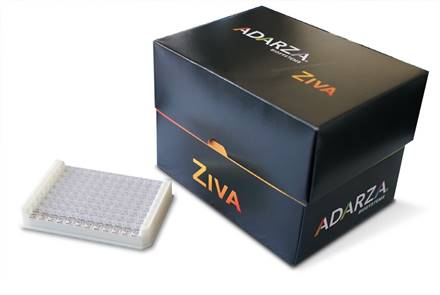
Adarza’s new protein multiplex instrument ZIVA
What were the key challenges your lab was facing?
Nanette: In the last 2 years, our company has undergone a great transformation. Our progress towards launching a product to market requires us to shift our primary focus from research to customer-based activities. The key transformation our company faced was transitioning from research to product development which required increasing the throughput of our manufacturing process and implementing a quality system. We needed to capture data at every step of our manufacturing process- from raw reagents to a finished product. As we ramped up capacity and throughput, traditional methods of recording our work and monitoring our quality were not sufficient. Most of our data were saved in a decentralized fashion, in individual or department folders, that did not lend itself to trending of any kind. As a company, we sought a solution that would allow us to have a centralized structure that enabled employees to optimize our processes quickly by making data-driven decisions.
Why did you choose Labguru?
Nanette: We chose Labguru because it fits our requirements as a startup in terms of infrastructure, timelines, features, and integration capabilities. Labguru fit our lack of infrastructure and timelines as a startup by providing a SaaS (Software as a Service) that was started immediately and hosted in the cloud. Its features for LIMS and ELN capabilities are exactly what we needed along with inventory tracking. Also, Labguru has REST services that we can integrate with our code. This enables our systems to synchronize processes and provide data integration bi-directionally. Finally, Labguru has been great to work with on resolving any needs we have beyond their current functionality from support to custom requirements.
What was your overall goal when you started using Labguru?
Nanette: We had two goals that we wanted to meet: The first one was very straightforward: we wanted a system that enabled us to manage a consistent inventory of the correct items for our labs, as well as not to run out of inventory items when most critical. Labguru provided this functionality using the shopping list, as well as the options to inventory items specific to its bio-collection. Users were able to add items to the shopping list triggering our purchasing manager to order items right on time. This sounds simple, but it is critical for a startup. We cannot afford to lose time due to manufacturing stoppages because we are short on material.

Labguru Shopping List feature
The second goal and most important one- We needed a Laboratory Information Management System (LIMS) for data management and traceability for processes upstream. The Labguru support team helped us leverage the Protocol’s Form Element feature to provide our team with templates where they could enter pertinent information easily and consistently. Additionally, Labguru’s development teams delivered the ability to connect Labguru data with our internal database. Within the first few months of building traceability in Labguru, we went from mining Excel spreadsheets to create graphs we’d paste on the wall for trending, to leveraging Labguru-captured information and creating visualizations in minutes that gave us the ability to make our next move.
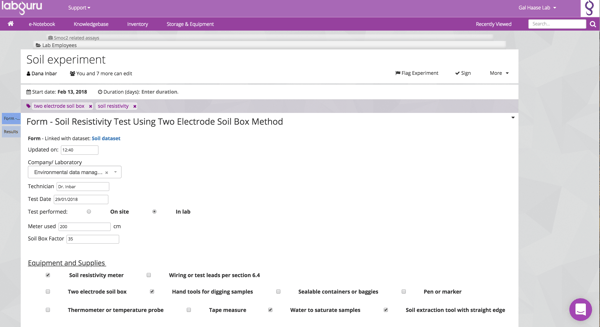
Form Element Feature- Labguru ELN
How did Labguru help you?
Nanette: Labguru’s ease of use is phenomenal. We were able to begin creating forms to build our workflow’s traceability in no time at all! Within three months of purchase, we were able to launch our preliminary structure and begin to gather data at each step of the manufacturing process. Within five months of purchase, we began populating inventory in the system and streamlining our communication when placing orders as well as ensuring we were ordering the right product every time. Labguru quickly replaced our e-mail and Excel-based system.
Labguru helped us by, well, helping us! From day one, we needed to connect Labguru to our local database. The Labguru development team worked with us to create this solution quickly. In addition, the support we get from our Labguru hero, Meirav Matto, is unparalleled. In cases where we can’t find an answer to our questions mining Labguru articles, the chat function allows us to send a quick note to support to get some help. Even though we are many time zones apart, the help comes swiftly and collaboratively. We can count on getting creative solutions to problems and new ways to use the software. In addition, we are often asked for feedback or upcoming challenges we might face. Those conversations give us confidence that Labguru will continue to grow with us in the future. Meirav and her team help us feel like we have a partnership with Labguru, not a customer/provider relationship.
What Labguru features do you like most and find critical for your work?
Nanette: One of the features that we love here at Adarza is the hearts and snowflakes on our login page! We look forward to it all year.
The Protocols module functionality is very easy to use and versatile. The Form Element feature allows linking between data entries and our inventory samples. Once our scientists enter data, it is populated in our database and our visualizations so that we can make decisions in a snap.
The other feature we enjoy is the ability to add equipment, samples, and reagents. It allows our researchers to link specific targets or equipment to their experiments easily, giving them the ability to search by target or equipment and see when it’s been used, and all the details associated with that experiment. This has been particularly helpful in equipment control change and maintenance. In addition, collaborators who are not necessarily involved in the day-to-day activities in the lab can also search by a target to keep abreast of what’s going on. Labguru’s ease of accessibility to data supports our need to make data-driven decisions which is a critical aspect to our growing company.
Has your team communication improved?
Nanette: Cross-team communication has improved in at least three different ways due to Labguru implementation.
- The centralization of data has allowed us to make informed decisions from one set of data. In the past, different people had different information and discussions. Despite everyone’s best intentions, different conclusions or assumptions were made about problems within pockets of people on the team.
- Labguru’s Shopping Cart functionality allows us to request items easily and allows us to see the status of an order by taking a glance at the Purchasing Manager’s shopping cart. In the past, when requests were email and Excel-based, it was challenging to find the information and understand the status of an order.
- The ability to link experiments to equipment has been instrumental in ensuring we know we have reliable machinery. The performance of preventative maintenance was tracked in a team folder but was difficult to find. Moreover, with the advent of our change control efforts, it was challenging to track any changes that occurred on an instrument. We kept paper documentation in the lab by each instrument, but decentralization made it hard to get information quickly. Keeping both of those records in Labguru makes it easy to find, ensures that information is collected in a standardized fashion, and allows us access to all of it in a few clicks.
How do you deal with raw research data and how does labguru help you with that?
Nanette: At Adarza, the bulk of our data in manufacturing is used to gather design history for our internal product, as well as to troubleshoot issues upstream of our process. Labguru’s functionality allows us to gather data in a uniform, centralized manner within folders, experiments, and datasets. Labguru allows us to connect data collected in datasets to a data warehouse where information is fed into custom visualizations. Those visualizations help us make decisions that support our ability to increase our manufacturing product quality and assure the internal research and development team we are feeding them products that support their optimization goals.

Creating Datasets in Labguru
Can you describe the ROI you see from Labguru?
Nanette: Aside from the obvious cost avoidance we gain by leveraging the inventory notebook functionality Labguru offers, the biggest ROI we’ve seen is in the ability to leverage the Protocols Form Element functionality to track our processes. Tracking who did what, and when, along with tracking all the small parts and their positions throughout the process has allowed us to detect problems and quarantine them from our internal research and development team. Most importantly, internal product traceability gives us the ability to trend information to track performance and support process improvement projects when needed. The metrics we can generate by compiling this data have supported the initiative to decrease our cost of goods in manufacturing by 60% which will improve our net revenue, increase our margins, and help us compete in our market.
To learn more about Labguru
Read more blog posts: